Aggregate Physical Properties Test
A total of 11 physical properties tests were conducted on both granite and sedimentary rock aggregate, which are: Gradation Test, Fines Content Test, Particle Density Test, Water Absorption test, Flakiness Index Test, Aggregate Crushing Value, Ten Percent Fines Value, Aggregate Impact Value, LA Abrasion, Drying Shrinkage and Organic Impurities Test
Of these tests, we will elaborate on the Aggregate Crushing Value Test, Aggregate Impact Value Test, Ten Percent Fines, and Gradation Test, as due to time constraints, these were the tests that we were able to conduct by ourselves. The rest of the testing was conducted by Samwoh.
AGGREGATE CRUSHING VALUE.
The apparatus consists of: a steel cylinder with a plunger that fit inside the steel cylinder, a base plate, a metal measuring cylinder, a tamping bar, and 2.36mm sieve, and compressive machine. The material used is aggregate that passed through a 12.70mm sieve but retained on a 9.52mm sieve. Aggregate is added in the measuring cylinder in 3 layers. For every layer added, the tamping rod is used to tamp the aggregate 25 times. The aggregate is weighed (M1) and transferred to the steel cylinder, which rests on the base plate.
The plunger is then placed over the cylinder and the entire set up is placed in a compressive machine. The compressive machine is loaded at a uniform rate such that 40kN is reached in 10 min. After which, the aggregate is removed. The aggregate is sieved with a 2.36mm sieve, and mass aggregate that passes through sieve is recorded (M2). The Aggregate Crushing Value is calculate as the percentage of aggregate that passes through the sieve over the total mass of aggregate.
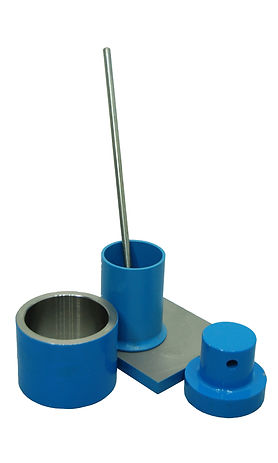
TEN PERCENT FINES
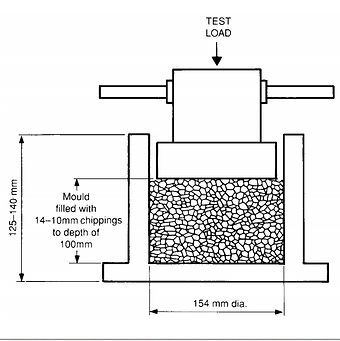
AGGREGATE IMPACT VALUE
The apparatus consists of a steel test mould with a falling hammer as shown on the right. The falling hammer has a mass of 13.5kg, and the distance from the hammer to the aggregate is 350mm. The material used is aggregate that passed through a 12.70mm sieve but retained on a 9.52mm sieve. The aggregate weighed (M1) , is added into the cup and is compacted by tamping it with a tamping bar 25 times. The aggregate is subjected to 15 blows of the hammer, each being delievered at an interval of not less than 1s. The crushed aggregate is then sieved over a 2.36mm sieve and the aggregate that passed through the sieve was weighed (M2). Aggregate Impact value is the percentage by mass of M2 over M1.
The Ten Percent Fines Test is highly similar to the Aggregate Crushing Value, and the apparatus used is the same. The material used is aggregate that passed through a 12.70mm sieve but retained on a 9.52mm sieve. Aggregate is added in the measuring cylinder in 3 layers. For every layer added, the tamping rod is used to tamp the aggregate 25 times. The aggregate is weighed (M1) and transferred to the steel cylinder, which rests on the base plate.
The entire set up is placed in a compressive machine and a uniform force is applied over 10 min such that the penetration rate is 15mm. The aggregate is removed and sieved over a 2.36mm sieve. The aggregate passing through the 2.36mm sieve is weighed (M2) and expressed as a percentage of M1. If this percentage falls within 7.5 - 12.5%, Ten Percent Fines Value is calculate by:
14x / (y + 4)
Where x is the maximum force used in kN, while y is the percentage of M1 / M2. If the percentage obtained falls outside the range the test has to be repeated. Two acceptable Ten Percent Fines tests have to be conducted on the same aggregate, and average is obtained.
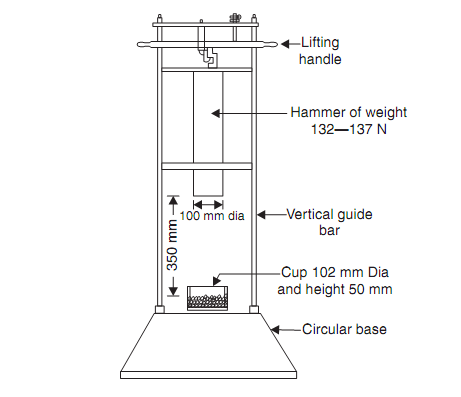
GRADATION TEST
Gradation test is used to determine aggregate particle size distribution. The apparatus needed is a vibrating table, and a sieve set, consisting of sieve sizes: 20mm, 14mm, 10mm, 6.3mm, 3.35mm, 1.18mm, and 75 micrometres. The sieves are stacked onto the vibrating table. A well mixed aggregate sample is weighed for its mass and then transferred to the sieve at the top with the largest size. The vibrating table is turned on to allow the aggregate to be sieved for 8 min.
Once the sieving process is completed, the sieves are removed and the aggregate in each sieve is weighed, and calculated as a percentage of the total aggregate mass. The particle size distribution is plotted in a graph as shown below, and the aggregate passes the gradation test if the graph plotted falls within the limits as shown.


Concrete Physical Properties Test
PREPARATION OF CONCRETE BLOCKS FOR TESTING
9.9kg of cement, 12.88kg of sand, , 20.56kg of granite rock and 4.0kg of water is weighed and placed into separate containers. All of the granite rock and sand are added into the concrete mixer, and aggregates are spread evenly.
The mixer is started and allowed to run for 30s. After 30s while the mixer continues to run, half the mass of water (2kg) is added evenly into the concrete mixture for 15s. The concrete mixer is stopped and covered to prevent moisture from escaping. The mixture is left to rest for 10 min. Prepare 64.35mL of Chemical Admixture M150 and 54.45mL of Chemical Admixture 85RA. Add the two chemical admixtures into the remaining 2kg of water. After 10 min, add the cement evenly into the concrete mixture. Then, start the mixer.
After 30s of the mixer running, stop it and use the scraper to clean off any material adhering onto the mixing blades or the walls of the mixer into the mixer pan. Then recommence mixing.
Add in the remaining water and chemical admixtures. Let the mixer run for another 2 min.
After 2 min, stop the mixture and pour all of it into a wheelbarrow. The above procedure is repeated for the sedimentary rock concrete, by replacing granite rock with sedimentary rock
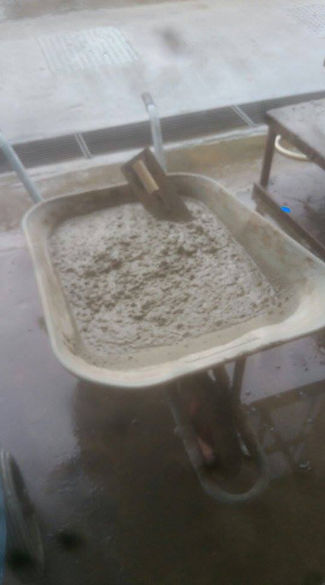
SLUMP TEST

A Slump Test is used to check the workability of fresh concrete by measuring its consistency, done by observing the subsidence of concrete due to gravity.
The slump cone is placed on a hard and sturdy metal plate. Fresh concrete is scooped into the cone in 3 layers. For every layer added, the tamping rod is used to tamp the concrete 25 times. The slump cone is then slowly lifted upwards to avoid disturbing the concrete cone. The concrete cone is allowed to subside due to gravity, and the result is known as concrete slump. The distance from the top of the slump to the top of the cone is measured. A measurement of more than 150mm would mean that the concrete is too wet and has low workability
CONCRETE MOLDING
The concrete has to be molded into cubes for compressive strength test, and cylinders for the tensile strength.
Molds are secured onto a vibrating table, so that air in the concrete mixture can escape due to vibration of the molds. Fresh concrete is scooped and placed into the molds such that it occupies a third of the mold’s volume. The molds are then allowed to vibrate for 1 min to allow air in the concrete to escape. This is then repeated twice more so that the molds are filled with concrete. The vibrating table is then turned off and molds are taken off.
The molds are scraped using a scraper to remove excess concrete to ensure the concrete has a smooth surface and is level with the opening of the molds. The concrete is then covered with plastic to minimize moisture loss. It is then left for 24h for concrete to harden, and demolded on the next day. Concrete blocks are then stored in water until testing
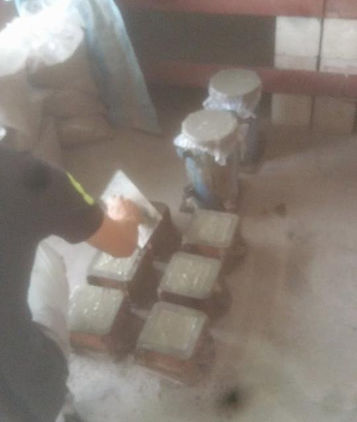
The Concrete Samples are then tested for Compressive and Tensile Strength
COMPRESSIVE STRENGTH
Compressive strength is the ability to withstand a compressing load. The compressive strength of the concrete was measured by placing the concrete cube in between the plates of the compressive machine. A load was gradually applied until the concrete buckled and the maximum load was recorded by the machine. Compressive strength is calculated by:
Max Load / Area of Concrete Cube.


TENSILE STRENGTH
Tensile strength refers to the maximum force required to "pull" the concrete until it breaks, and for our testing we used the indirect tensile strength test because the apparatus required is simpler, and the tensile strength is derived from the compressive strength. Just like the compressive strength test, the maximum load is obtained from the compressive machine, and the tensile strength is derived from this formula: (2 x Failure Load) / π x Diameter x Thickness)
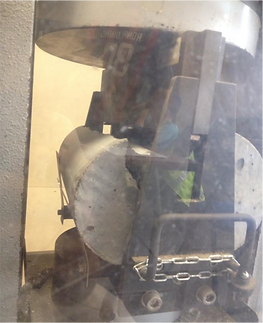
Tests on Methods to Mitigate
Alkali - Silica Reaction
The testing follows the criteria laid down by ASTM C1260. The materials used are as follows: sedimentary rock, cement, fly ash, lithium chloride, 1M NaOH solution, water. The apparatus used are as follows: Concrete mixer, Comparator, Molds for Mortar Bars, Scrapper.
Prepare 440g of Ordinary Portland Cement, 990g of sedimentary rock with a specified gradation, and 206.8g of water. Add the water and then the cement into the mixing bowl and attach it to the concrete mixer. Start the mixer and mix at slow speed (140 r/min) for 30s. Add all of the sedimentary rock over the next 30s period, while still mixing at slow speed
Stop the mixer, change to medium speed (285 r/min) and mix for 30s. Stop the mixer and let the mortar stand for 90s. During the first 15s scrape down any mortar that collected on the side of the bowl. After 90s continue to mix the mortar at medium speed for 60s.
Compact the mortar into 3 steel moulds, each mould with the dimension 25mm x 25mm x 280mm, therefore making 3 mortar bars. Cure the mortar bars for 48 hours. Take measurements of the dimensions of the mortar bars using a comparator. Store the mortar bars in a 1M NaOH solution at 80 deg Celsius for 14 days. Take measurements of the mortar bars every 2 to 3 days with the comparator and record the measurements.
For the production of mortar bars with fly ash, repeat the above procedure, but replace 25% of cement by mass with fly ash. Add the fly ash in together with the cement.
For the production of mortar bars with fly ash and lithium chloride, repeat the above procedure, but replace 25% of cement with fly ash, and add in 1.6g of lithium chloride. Lithium chloride and fly ash to be added in together with the cement.
As an expansion of less than or equal to 0.10% after 14 days is indicative of innocuous aggregate, this will be our target to meet when testing the inhibiting effects of fly ash and lithium chloride.
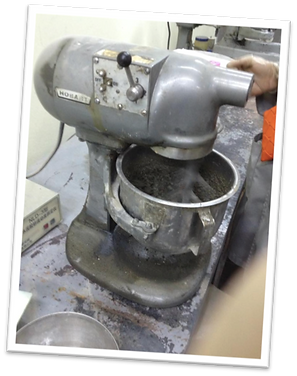
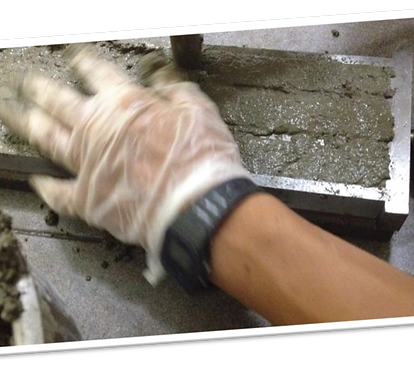